Introduction
The development and distribution of orthopedic implants—such as joint replacements, spinal devices, and fracture fixation systems—require adherence to a complex web of regulatory standards worldwide. As the demand for these life-enhancing medical devices grows, manufacturers must navigate diverse compliance frameworks to ensure patient safety, product efficacy, and market access. The Global Orthopedic Implant Materials Compliance Guide serves as a critical resource for stakeholders aiming to align with international regulations while fostering innovation. This article outlines key considerations outlined in the guide.
The Importance of Compliance
Orthopedic implants are classified as high-risk medical devices due to their direct interaction with human tissues and long-term implantation. Regulatory bodies prioritize rigorous testing, material traceability, and post-market surveillance to mitigate risks such as infection, mechanical failure, or adverse biological reactions. Non-compliance can result in costly recalls, legal liabilities, and reputational damage.
Regional Regulatory Landscapes
The guide emphasizes the need to understand region-specific requirements:
- United States: The FDA oversees device classification (Class I-III) under the Federal Food, Drug, and Cosmetic Act. Premarket approval (PMA) or 510(k) clearance is mandatory, with strict guidelines for biocompatibility (ISO 10993), sterilization (ISO 11135), and clinical data.
- European Union: The EU Medical Device Regulation (MDR 2017/745) enforces conformity assessments by Notified Bodies, emphasizing clinical evaluation, risk management (ISO 14971), and post-market monitoring. Materials must meet General Safety and Performance Requirements (GSPR).
- China: The NMPA (National Medical Products Administration) mandates registration certificates and localized testing for most implants. Recent reforms prioritize alignment with international standards while retaining unique documentation requirements.
- Emerging Markets: Countries like India, Brazil, and Saudi Arabia increasingly adopt ISO-based frameworks but may impose additional certifications or local manufacturing mandates.
Orthopedic Implant Materials – Specific Challenges
The choice of implant material—titanium alloys, cobalt-chrome, polymers, or bioresorbables—directly impacts regulatory pathways. Key considerations include:
- Biocompatibility: Testing for cytotoxicity, sensitization, and genotoxicity per ISO 10993.
- Mechanical Performance: Fatigue resistance, wear rates, and compatibility with imaging technologies (e.g., MRI).
- Surface Modifications: Coatings (e.g., hydroxyapatite) or porous structures may require separate evaluations for osseointegration and long-term stability.
Documentation and Labeling
Comprehensive technical documentation—including design history files (DHF), risk assessments, and clinical evidence—is essential for audits. Labeling must comply with local languages, units of measurement, and symbols (e.g., CE marking). Unique Device Identification (UDI) systems are now mandatory in major markets to enhance traceability.
Post-Market Obligations
Regulators increasingly focus on post-market surveillance. Manufacturers must implement systems for adverse event reporting, periodic safety updates, and proactive risk management throughout a product’s lifecycle.
Strategies for Success
The guide highlights actionable steps to streamline compliance:
- Early Engagement: Collaborate with regulatory consultants during R&D to identify material and testing requirements.
- Harmonized Testing: Leverage internationally recognized standards (e.g., ASTM, ISO) to reduce redundant evaluations.
- Digital Tools: Utilize AI-driven platforms for real-time regulatory updates and gap analysis.
- Sustainability: Align with emerging regulations on recyclable or eco-friendly materials.
Conclusion
The Global Orthopedic Implant Materials Compliance Guide underscores that regulatory compliance is not a barrier but a strategic enabler. By understanding regional nuances and adopting proactive quality management systems (QMS), manufacturers can accelerate time-to-market, reduce costs, and—most importantly—deliver safer solutions to patients worldwide. As material science evolves, so too must the frameworks governing these innovations, ensuring that compliance keeps pace with technological advancement.
About Lyntop Medical
Lyntop Medical offers comprehensive contract manufacturing solutions that empower your brand and improve patient lives. With deep expertise in navigating global regulatory standards—from FDA submissions to EU MDR compliance—we specialize in transforming innovative concepts into market-ready orthopedic implants. Our end-to-end services include material selection, prototyping, sterilization validation, and scalable production, all backed by ISO 13485-certified quality systems.
We understand the challenges of bringing groundbreaking medical devices to market, from biocompatibility testing to post-market surveillance. By partnering with Lyntop Medical, you gain a reliable ally committed to precision, transparency, and patient safety. Let us handle the complexities of compliance while you focus on advancing healthcare. Together, we turn regulatory hurdles into opportunities for global impact.
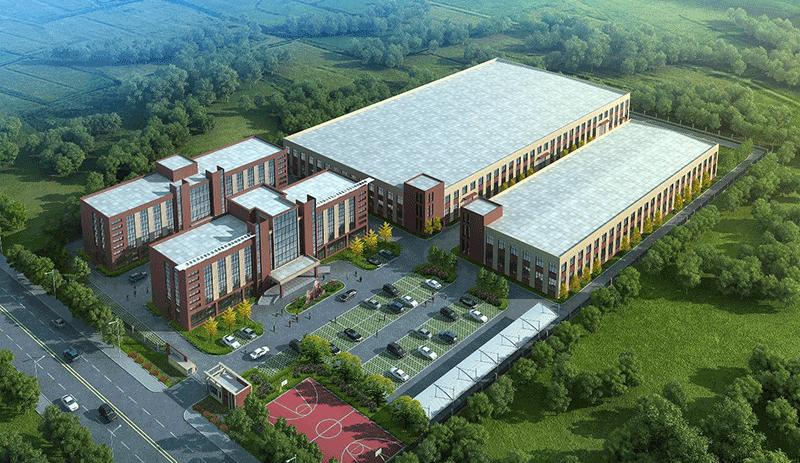